Around the 17th century, colonization gave many European countries access to new techniques and innovative ways to produce more durable fabrics. They could therefore be printed and washed without fear that the pattern would be damaged in the process.
The British imported most of their patterned cottons from India. Although initially they commissioned specific designs – significantly more subdued than traditional Indian designs – to be developed in India, they later adapted the newly acquired knowledge and started printing themselves. In 1676, a French refugee opened the first English printing press, located near London.
Since the middle of the 18th century, the English have been printing on fabric using the screen printing technique. This technique was perfected in the early 1900s and it was then called serigraphy. But it was really at the beginning of the 1930s that the technique was perfected to its maximum, producing prints intended for furnishing in Art Nouveau or Art Deco styles, or even prints on fabric intended for clothing fashion. Subsequently, around 1950, the frame printing technique was mechanized to increase production capacity. It is still used today, but more for artistic and recreational purposes. However, the process was quickly replaced by rotary printing, which proved to be more efficient and significantly faster. Then, a new technology appeared: digital sublimation printing on fabric.
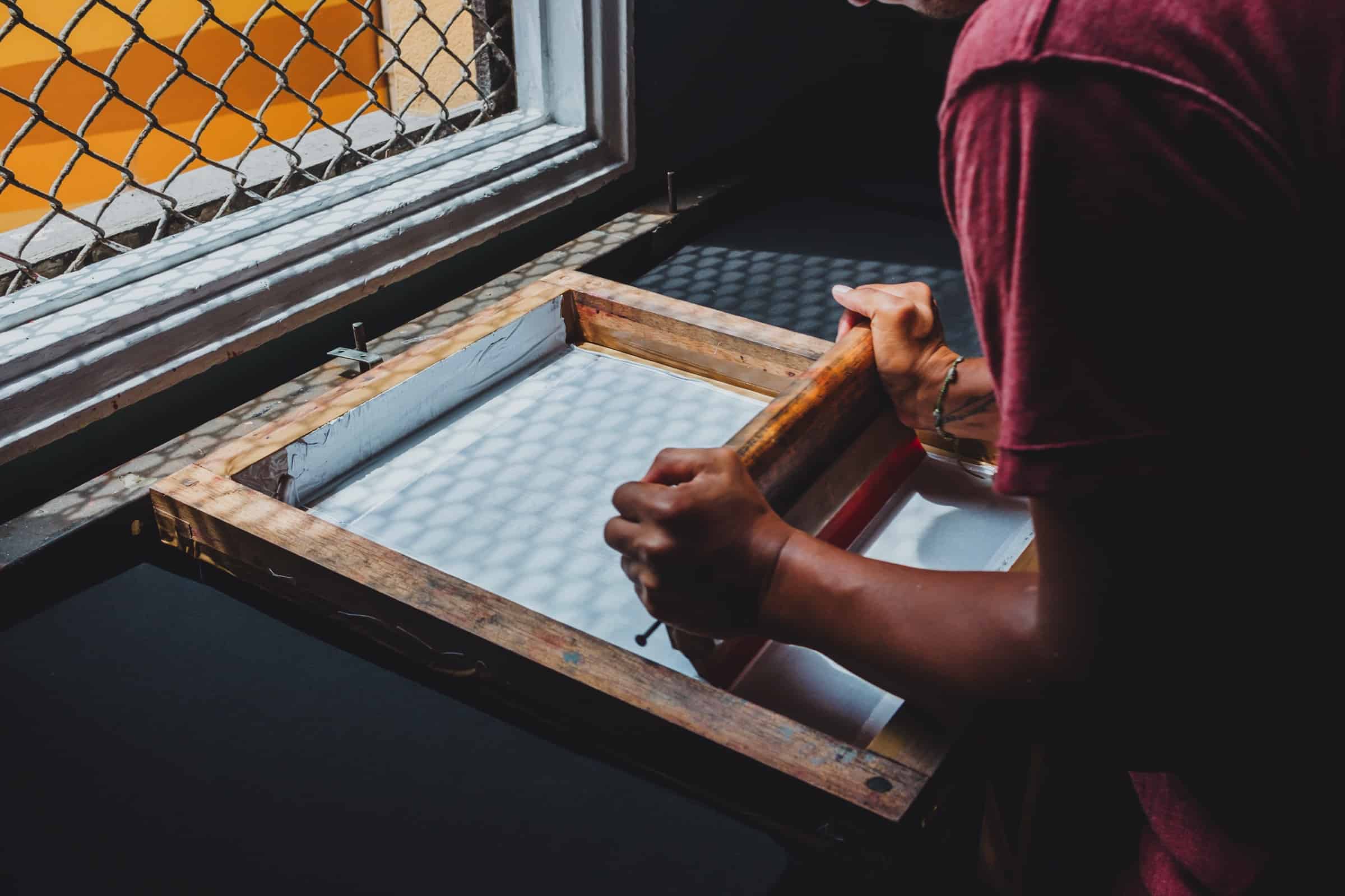
Indeed, it was not until the 1980s that the first form of digital printing was developed, forever changing the way the textile industry operated and opening up a world of new possibilities for established designers or those budding. This revolutionary technique uses computerized lasers that inject ink directly into the fabric.
The introduction of sublimation printing in the 1990s only pushed the changes further, making artistic expression in terms of designs virtually limitless.
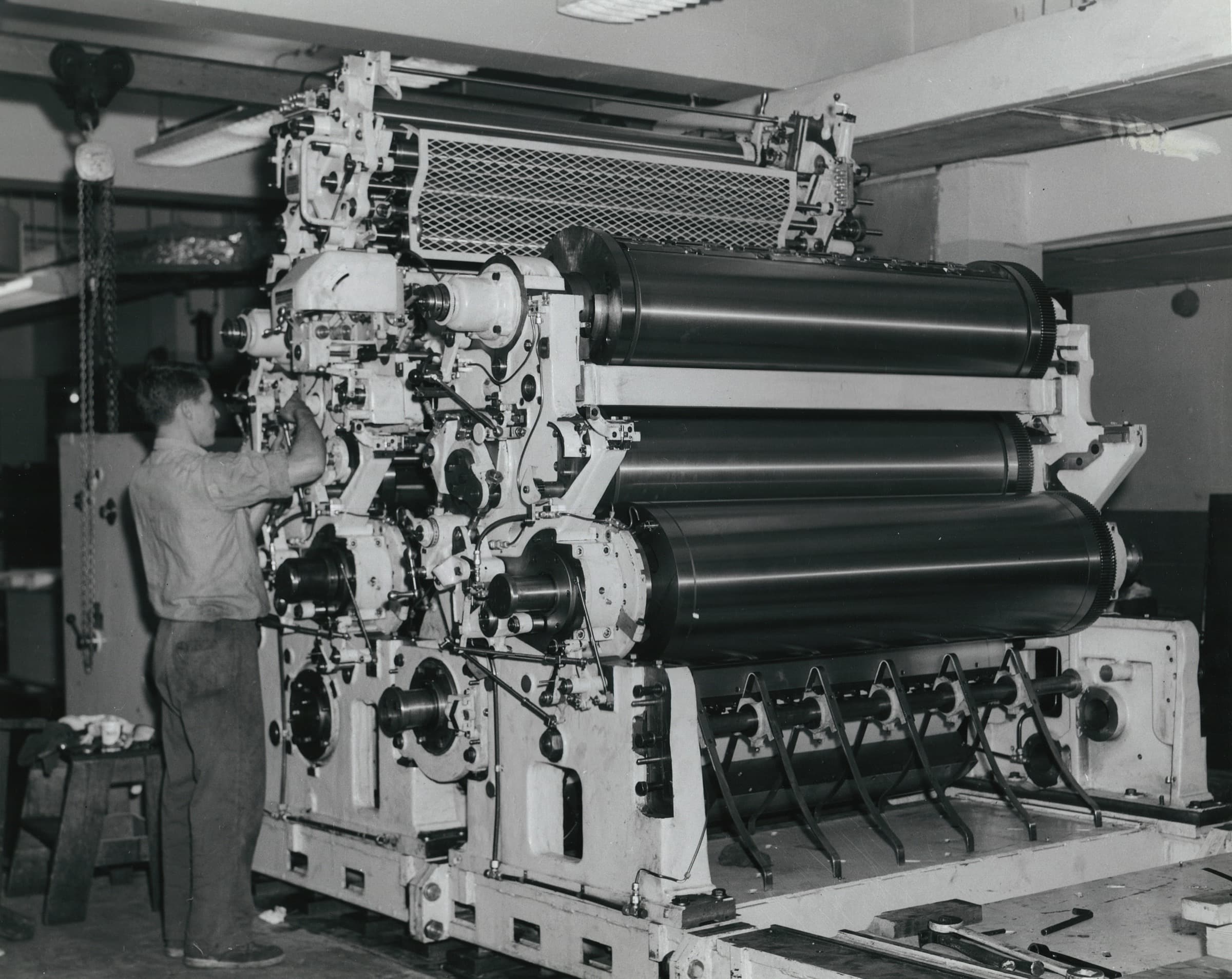
Although it is now much easier to transfer a vision to fabrics thanks to new technologies and advanced machinery, the artistic factor of the process is certainly not lost. In many places around the world, artisans often rediscover ancient methods – such as woodblock printing, for example – to give their creations a unique and authentic aura.
Source: https://www.matchymatchydesign.com/en/fabric-printing-history/
Research and innovation
In the 20th century, textile chemistry continued the stream of innovations of the previous century. Ease of use, gamut breadth and color fastness continue to improve. Marginal, but made famous by the printing of T-shirts, thermo-printing transfers dyes at high temperature. Appeared in the 1980s, it is mainly used for printing on synthetic media. Research is now highlighting inkjet technology, a large printer controlled directly by a computer.
20th century motifs, between creations and traditions
The history of textile printing is made of constant returns where designers seek inspiration in the archives of past centuries. The plants painted on the canvases of India which fascinated the society of the Ancien Régime have not finished being interpreted. The 20th century is no exception to this need to use old motifs: revivals and traditions feed the collections. A new function quickly grew, that of the stylist who developed trends, adapting shapes to market requirements. His choices, his advice determine the consistency of industrial styles, between tradition and creation.
Source: https://www.musee-impression.com/etoffes-impressiones-au-xxeme-siecle/