Throughout the world, the history of fabric printing is closely linked to that of dyeing. The first fabrics adorned with printed patterns appeared in the East several millennia ago.
In Europe, it was not until the modern era that craftsmen in turn embarked on the manufacture of printed textiles. The industrial revolution then allowed new printing techniques to emerge (roll printing, flat frame).
Today, digital printing and screen printing (flat screen or rotary printing) are the most widely used techniques.
Techniques dating back to Antiquity
Ancient civilizations felt the desire to color, personalize and embellish their fabrics very early on. Like dyeing, printing is a branch of textile finishing which was initially based on elementary processes. For a very long time, the art of printing patterns consisted of applying natural dyes to fabrics using stencils or engraved pieces of wood.
It is generally accepted that the peoples of India and Mesopotamia printed their textiles as early as the 2nd millennium BC. J.-C.
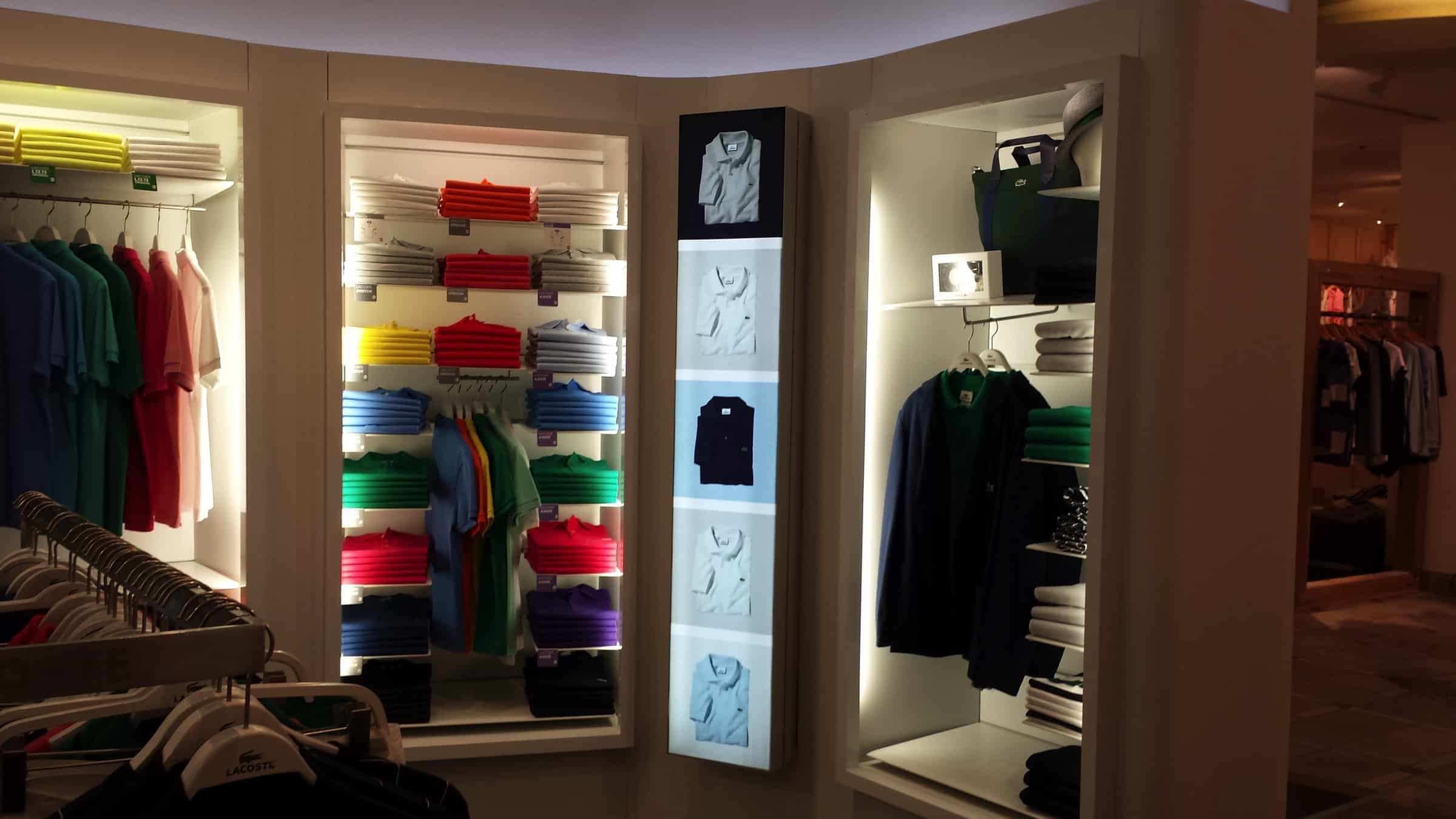
China, on the other hand, was already printing on silk using blocks of carved wood two centuries before our era, laying the foundations of block printing.
In the 7th century, Japan mastered the art of stencil printing… without suspecting that it was the ancestor of screen printing!
At the same time, other processes derived from dyeing and weaving have been developed on several continents to create handcrafted textile patterns.
The Indian women, the trigger for textile printing in the West
At the beginning of the 17th century, new maritime routes simplified trade between East and West. The cotton trade and the import of fabrics are developing on the European continent.

These “curiosities” from India, Siam, Persia or Japan are successful. Luxurious exotic silks (Damascus, Madras, Beijing, etc.) and more accessible “Indian” ones (white or block-printed cottons), seduce all social classes. The motifs of the Indian women show an advanced mastery of certain printing techniques (mordanting and reserve), a know-how still unknown to Westerners. They are also light, soft and easy to care for, so many advantages that set them apart from hemp, linen and heavy fabrics produced by the Lyon silk workers or the Royal Woolen Manufactures…
The first French printing workshop was created in 1648 in Marseille, others followed suit. All have the ambition to imitate these fashionable fabrics, but the quality is rarely there (clumsy patterns, poor color fastness to washing…). Despite everything, the growing popularity of Indian women worries the corporations already well established in France.
Louis XIV and his minister Louvois decide to act to protect the activity of French manufacturers. In 1686, a decision of the Council of State formally prohibited the trade, production and even the wearing of Indian women, without having the desired effect. Encouraged by the strong demand, the “indiannage” continues in a clandestine way. Throughout the Prohibition period, printing processes improved, leading to a lifting of the ban in 1759 and official control of production quality.
Subsequently, fabric printing techniques continued to evolve in France. Block printing was abandoned to make way for mechanical techniques around 1860. Then this ancient technique was revived by William M. Morris ten years later to found the English Arts and Crafts movement. This printing process continued in France until the middle of the 20th century.
Now, the modern fabric printing techniques are screen printing and sublimation.
Source: https://textileaddict.me/lhistoire-de-limpression-textile/