Given that the large format display industry serves communication agencies, advertising agencies, show organizers as well as large chain stores, it sometimes happens that the project management team of M&M Graphic has to juggle the unexpected.
Sometimes these are internal contingencies, which are easier to manage because the managers are present on site; but sometimes we face external contingencies over which we have little control.
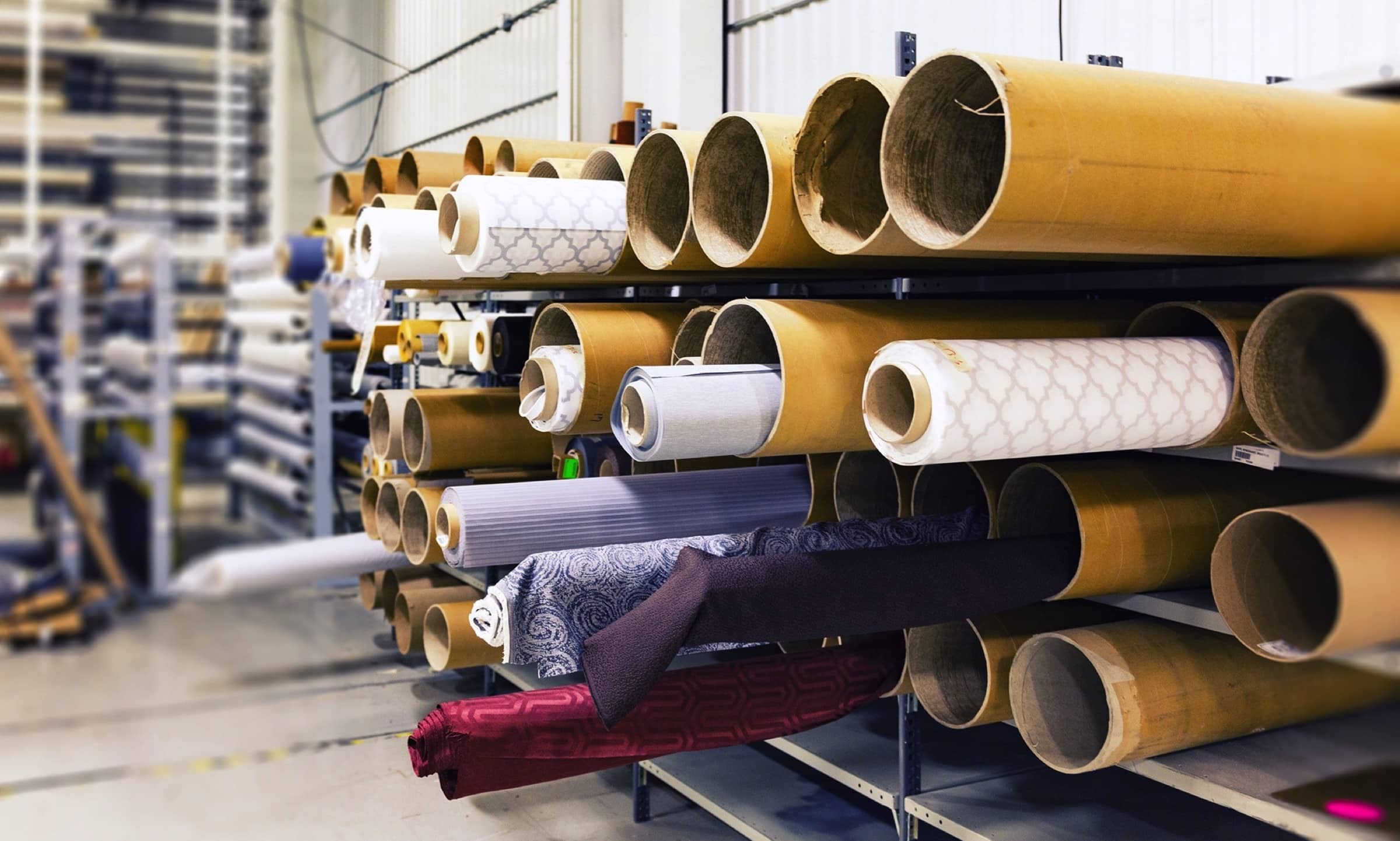
Internal contingencies
There are several kinds of internal contingencies. For example, the delivery of a fabric order that is late. This can happen on occasion. In this case, it is usually not a big problem because we keep equipment in reserve and often order in advance, before stocks are exhausted. This practice aims to respect the production deadlines promised to customers and to reduce unnecessary stress.
In addition, orders for structures from Asia and aluminum extrusions in Europe are delivered by container on freighters and often arrive between four and eight weeks later. It is therefore impossible to predict the exact date of arrival of the order at the production workshops.
On the other hand, as the work is done with machines, it is possible that breakage may occur. We must then either carry out the repair quickly with the teams in place if this is possible, or if necessary call a specialized technician urgently. Stopping a machine has the direct consequence of delaying the production deadline for certain orders. Even if everything is done to avoid it, it may happen that we have no choice but to inform customers of the situation and ask them for an additional delay. In most cases, customers are understanding and the extension is granted. On the other hand, the delivery time is sometimes non-negotiable due to major imperatives and we must respect this at all times. Since several machines operate in the workshop, we can still continue production by reorganizing the schedules, despite equipment failure.
External contingencies
Among the external contingencies, we can first name everything that is customer-related. That is to say the moment when his electronic file for the printing of his canvas is received, or the moment when he must send the structure to receive a new canvas, or his order form. We also talk about changes made during production, which are generally a source of delays. In order to guarantee as few unforeseen events as possible in exchanges with the customer, numerous follow-ups are carried out during the process, at each stage of order planning, then during production as such.
Apart from those coming from the customer, there are obviously other possible sources of external contingencies. Let’s talk about those caused by carriers. For example, if a delivery carrier picks up an order too late, or if it makes the delivery too early, or if it never shows up at the pick-up or delivery point, this will create a problem, since the customer will not receive their order on time. It is in order to carry out close follow-ups on the level of the planned deliveries that the delivery bill of lading number of an order is always added to the corresponding production file. Thus, it will be easy to trace at all times and in real time where an order is being delivered. This number also allows the customer to follow up himself if he wishes.
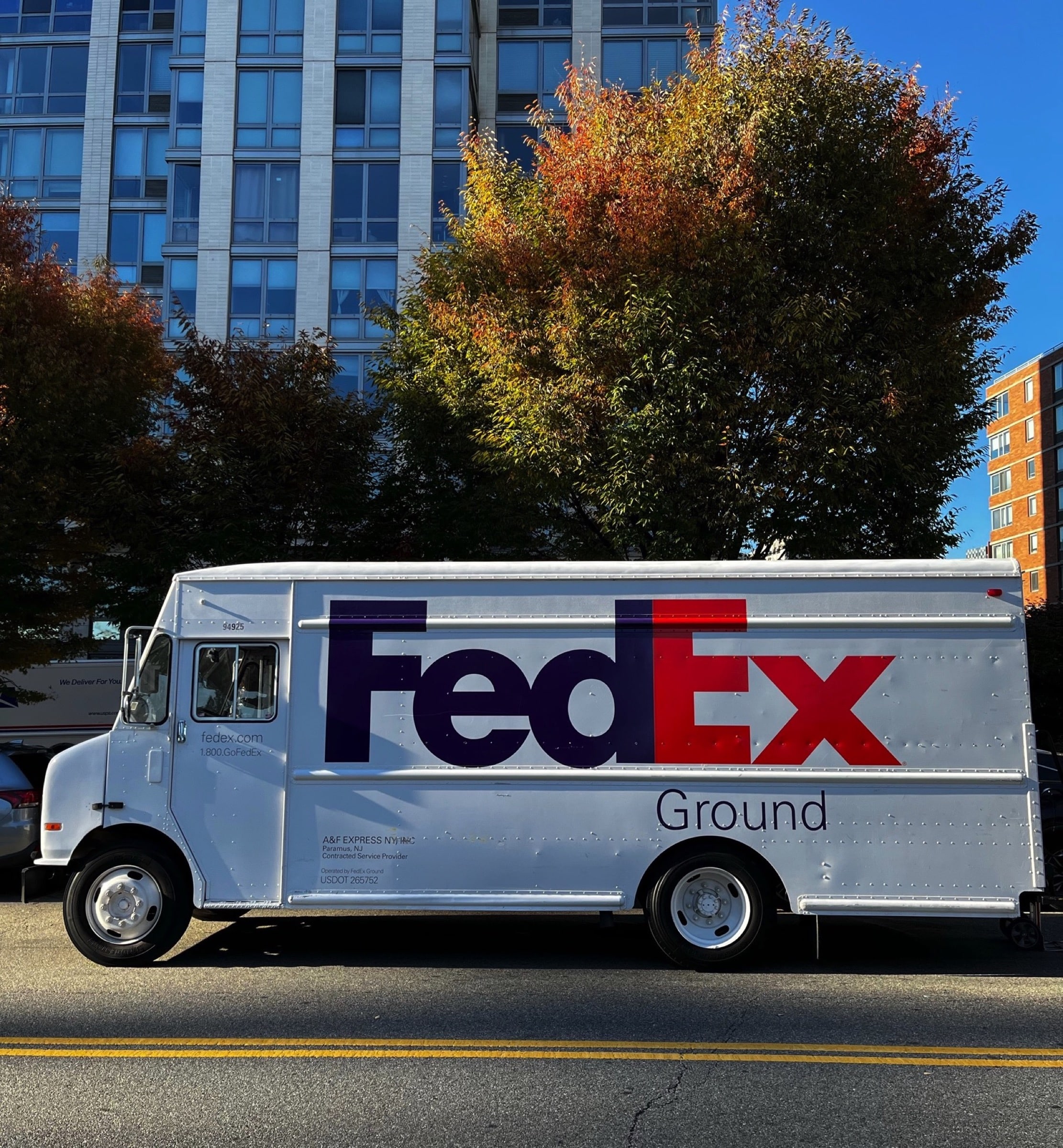