In large format display, it is often necessary to manufacture gigantic objects for advertisements, pieces of scenic decorations or even banners or light boxes that have unconventional shapes.
To achieve this, we must make plans or 3D drawings, detail each manufacturing step in advance, seek the advice of experts in various trades such as welders, machinist specialists, electricians, painters, costume makers, to name a few.
The giant Maxi bag of the 2019 contest
Sometimes, the customer provides his manufacturing plan with his drawings, but it also happens that the customer has nothing and that we have to help him a little. Once upon a time, a customer called and asked, “How could I make a giant Maxi bag 14 feet tall?” He especially wanted to know how to prepare his files for printing. He finally realized that it was quite easy: just take a normal Maxi bag, unsew it completely and make a scale pattern with this bag. Then, it was enough to produce it 10 times larger while maintaining the original proportions.
The bag in question can be seen in the photo above, which shows it in the shipping department. The garage door is 20 feet high, which gives a good idea of the size! The idea was that the bag would “walk” from town to town.
Each month, customers had to guess the amount of money equivalent to a bag full of food. The person who guessed the amount closest to the truth won a Maxi gift card of equivalent value.
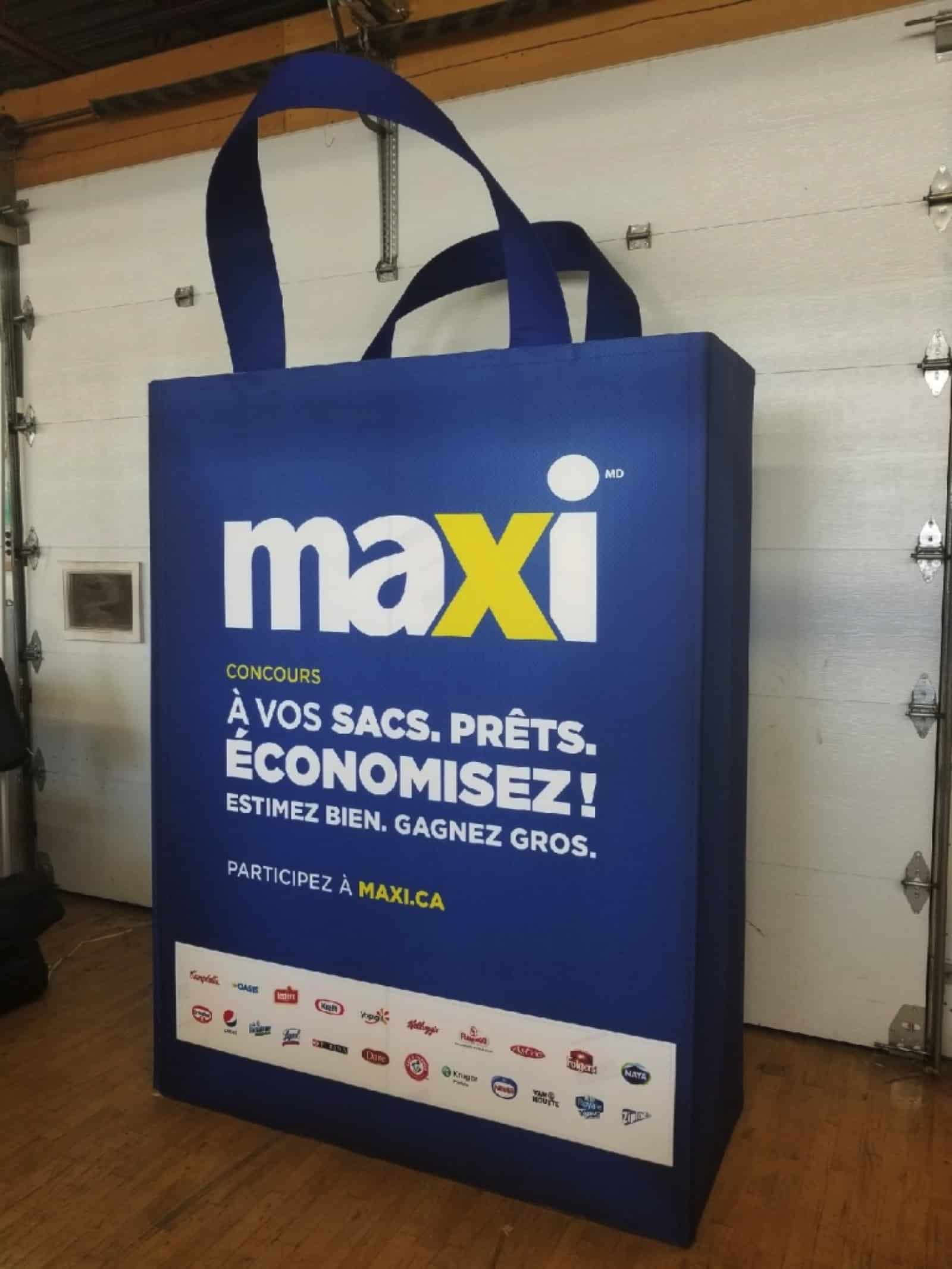
There is still a page on the Maxi website on this subject even if the contest is over: https://concours-en-ligne.ca/concours-web/14085_concours-maxi-a-vos-sacs-pret-economisez.
Round light boxes from Dolce & Santella in Laval
Another interesting special project is the round light boxes produced by M&M for a gellateria in Laval. Normally, square or rectangular light boxes are made, but not round. The reason is very simple: the extrusions are straight and do not bend. Without this, it is impossible to hold the printed canvases. You can, however, bend straight T-17 thin extrusion, but no company could do this in Quebec until last year. You had to go through Europe and pay high air delivery costs, which really increased the manufacturing costs too much.
We therefore used our creativity and found a specialist welder who owns several benders. After some testing, it was found that this supplier could bend the extrusions and form the structure of a beautiful circular light box, with a cross brace on top.
All that remained was to draw the box with its actual dimensions to provide a 3D plan to the customer. We had to make sure that once the two extrusions were welded at the top and bottom, there would be enough space left in the center to install the LED modules for the case lighting. Eureka! There was 1” of space left, which is enough.
The Quebec supplier manufactured the boxes impeccably! Despite the fact that these extrusions were anodized, he still managed to make beautiful welds inside the 4” aluminum bar that forms the outline of the case. You can see the structures of the round boxes in the photos below.
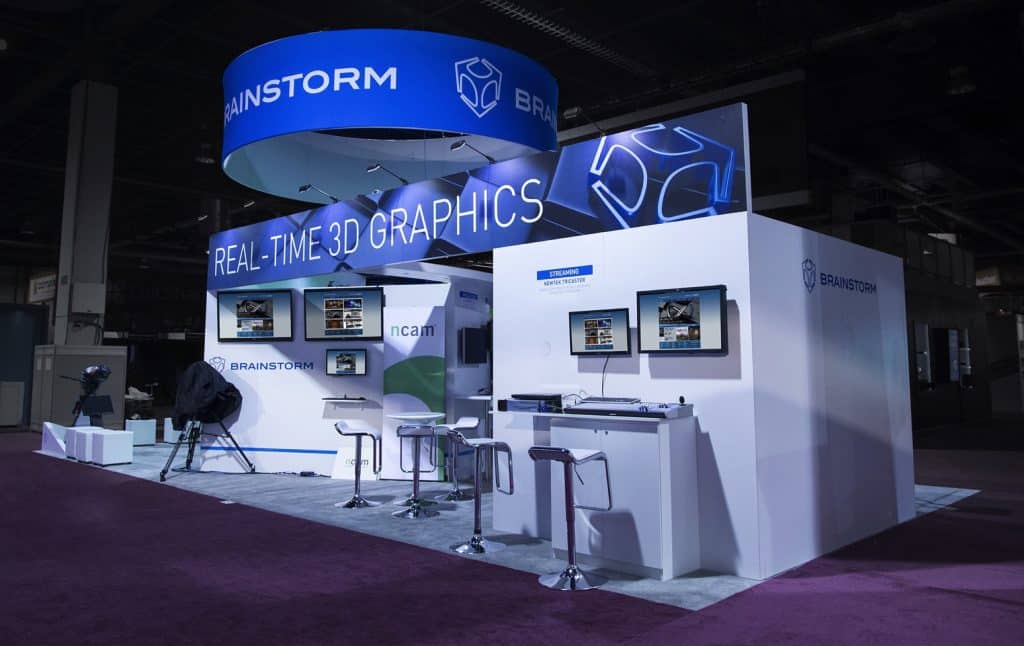
Then there was another challenge: finding the stretching recipes to apply for a round canvas. Usually, we produce square or rectangular canvases, of which we know the percentage of stretch in width and height. But with a round canvas, there is no “width” or “height”. So we had to do a lot of trial and error to finally come up with a recipe that works. We must therefore give the credit to the efforts of graphic designers and designers!