The origins
The history of textile printing is closely linked to the world of dyeing. The first printed fabrics originated in the East and date back several millennia. As one can imagine, the printing techniques of the time were rudimentary. Stencils or engraved pieces of wood were used to imprint designs on the fabric.
In India and Mesopotamia, it is generally accepted that artisans had been printing on textiles since the 2nd millennium BC.
In Europe, it was only in modern times that the first prints on fabric took place. The industrial revolution then allowed new printing techniques to emerge, such as roller or flat screen printing.
The first textile patterns that appeared during Antiquity
Humans have long developed a taste for decorating and coloring their clothes. In fact, at that time, wearing printed clothes was a sign of ennoblement.
In China, 200 years before our era, patterns were already printed on silk. The printing technique was rudimentary but very artistic. The craftsman had to carve a block of wood, coat it with dye and then transfer this dye to the fabric using a roller. Thereafter, it was necessary to wait for the dye to dry to repeat the process without risking spreading the dye to unwanted places. This way of doing things initiated the basis of block printing.
Later, in the 7th century, Japan became masters in the art of stencil printing. This technique was the ancestor of screen printing.
Block printing, the predominant technique until the 18th century
Textile block printing (woodcutting) involves engraving a raised design onto a board or block of hardwood, then coating it with a thickened coloring substance in order to use it as a stamp, using a mallet or press.
This process, already well known in the East in the Middle Ages, continued to develop in India, China and in the Rhine Valley between the 10th and 14th centuries.
“The Indians” trigger the beginning of printing in the West
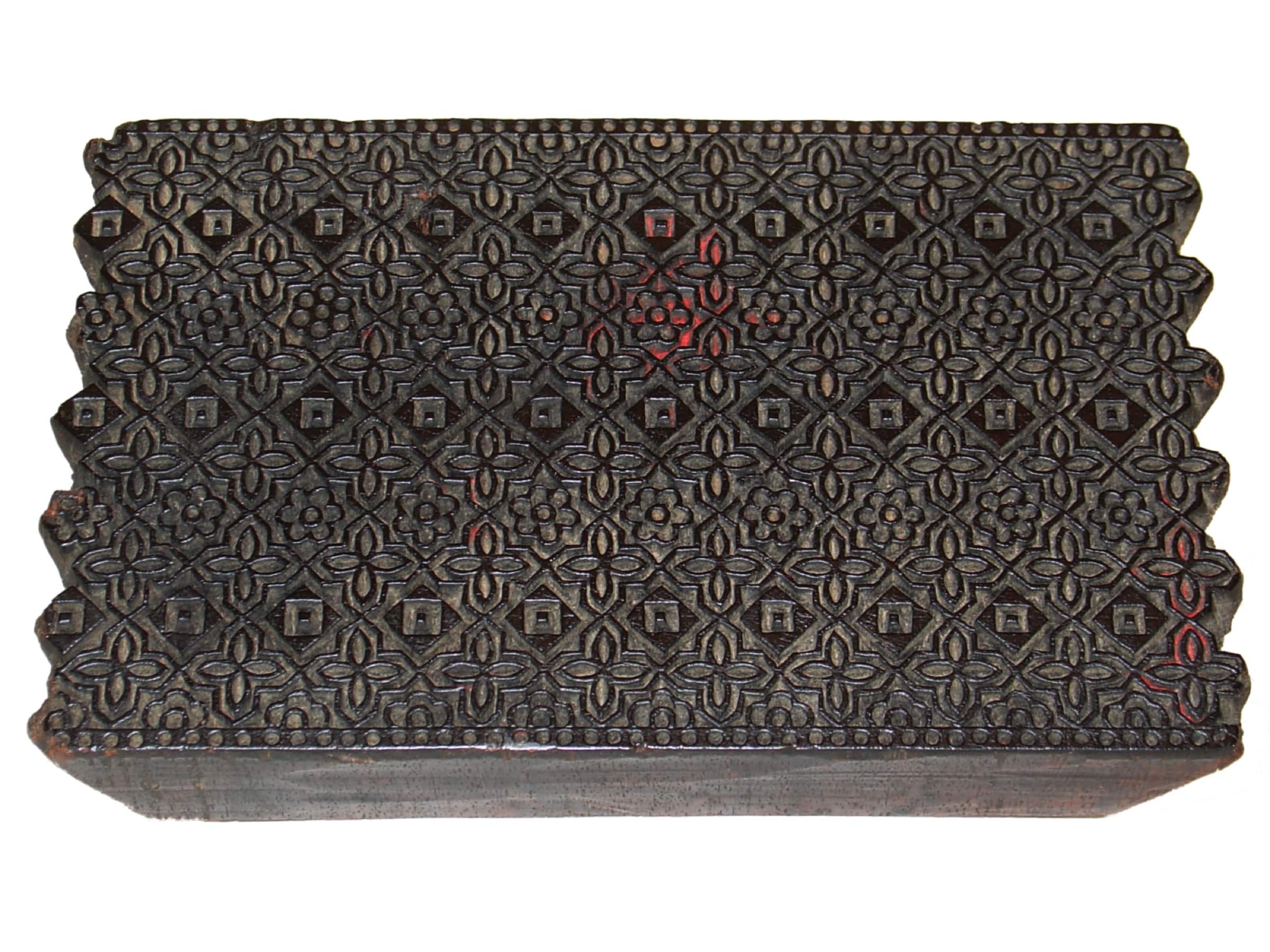
At the beginning of the 17th century, new maritime routes simplified trade between East and West. The cotton trade and the import of fabrics developed in Europe.
These “curiosities” which arrive from India, Siam, Persia or Japan are becoming very popular. Luxurious exotic silks (damascus, madras, peking…) and more accessible “Indian” (white or block-printed cottons), seduce all social classes. The motifs of the Indian women testify to an advanced mastery of certain printing techniques (mordanting and reserve), a know-how still unknown to Westerners at the time. They are also light, soft and easy to care for, so many advantages that set them apart from hemp, linen and the heavy fabrics produced by the Lyon silk workers or the Royal Woolen Manufactures.
It was in 1648 that the first French fabric printing workshop opened its doors in Marseille. Soon, several others followed in his footsteps and also started their own printing business. All aimed to imitate these fashionable fabrics, but the results turned out to be of poor quality (clumsy patterns, poor color fastness to washing, etc.) Despite everything, the growing popularity of Indian women worried corporations already well established in France.
This is why Louis XIV and his minister Louvois decided to act to protect the activity of French manufacturers. In 1686, a decision of the Council of State formally prohibited the trade, production and even the wearing of Indian women, without having the desired effect. Encouraged by the strong demand, the “indiannage” continues in a clandestine way. Throughout the Prohibition period, printing processes improved, leading to a lifting of the ban in 1759 and official control of production quality.
The Oberkampf of Jouy-en-Josas factory
The following year, in 1760, still in France, the famous Oberkampf factory in Jouy-en-Josas opened its doors and invented monochrome patterns. These motifs are drawings illustrating scenes from everyday life including men and women in period dress, horses, carts and farm animals. There are a variety of varieties and they are rich in detail. This factory offers a product of such high quality that it is officially chosen by the Royal Court (from the reign of Louis XV at the time). The factory was in operation until 1843. The production site was spread over 14 hectares, completely enclosed by walls and comprised 36 buildings. Then it closed its doors and the estate was sold in batches. The last large building was demolished in 1864.
The only remains that still exist today:
- the Maison du Pont de Pierre, the first house in Oberkampf;
- a wing of his family home, occupied by the town hall of Jouy-en-Josas;
- another wing of his family home, opposite the town hall, on the other side of avenue Jean Jaurès;
- the former Mill of Calenders, considerably modified by its transformation into a wheat mill and then into a chemical products factory now called Vieux Moulin.
To consult the Jouy-en-Josas Tourist Office website: https://www.jouy-en-josas-tourisme.fr/en/file/5532289/ancienne-manufacture-de-toiles/. The historic factory site is located 33 kilometers southwest of the city of Paris.
The end of wooden planks and the Arts and Crafts Movement
Ten years later, in 1770, wooden planks were replaced by copper plates. A short time later came the debut of cylindrical drum printing machines.
At the end of the 18th century, the entire territory had more than a hundred Indian cloth factories. Block printing is then the most used technique in France. It will be gradually supplanted by mechanical processes and will disappear in 1860… before reappearing 10 years later thanks to William M. Morris, publisher, printer and founder of the English Arts and Crafts movement.
The process lasted until the middle of the 20th century. Some workshops still have old wooden blocks in their possession and still use them to print exceptional series.
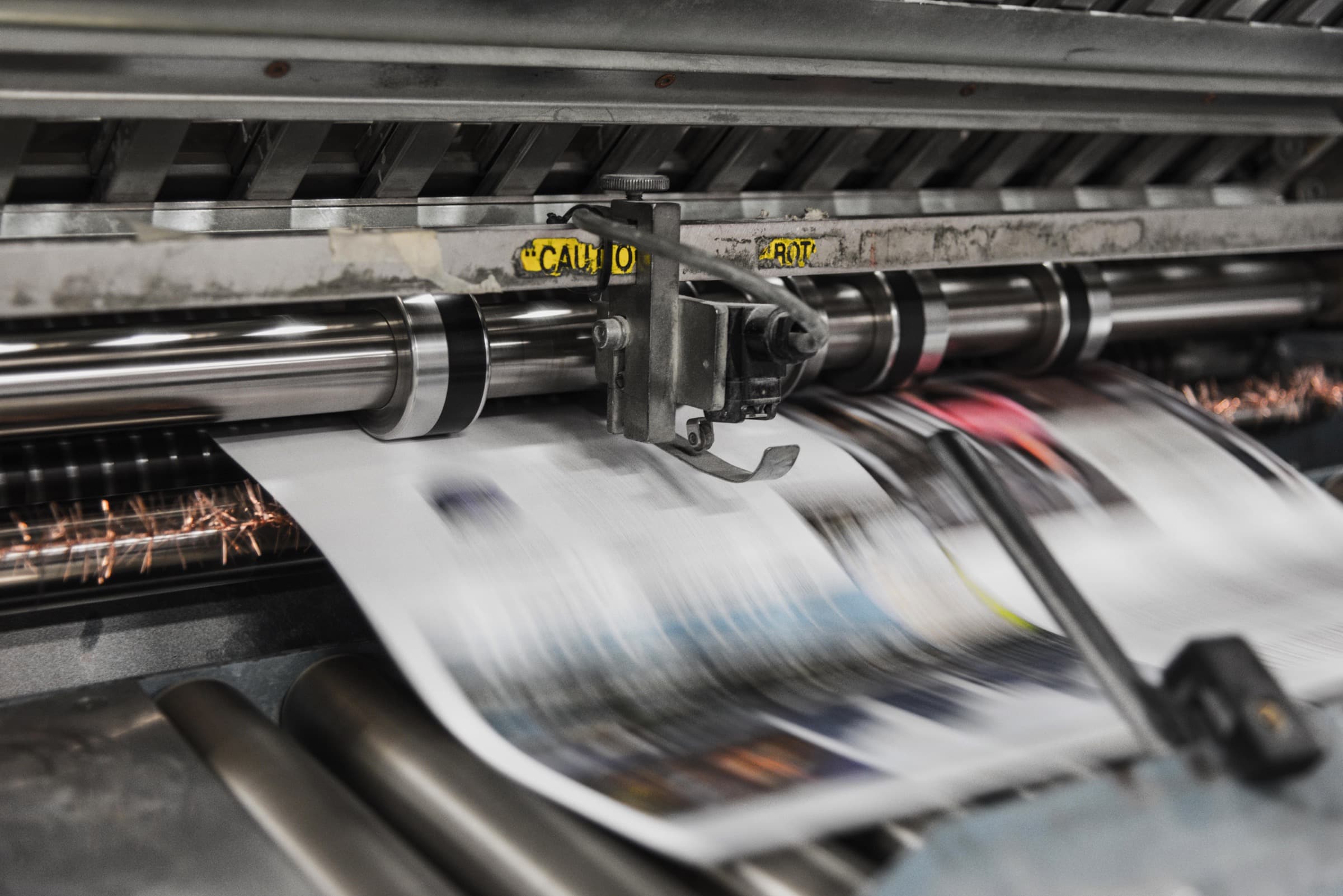
Source : https://textileaddict.me/lhistoire-de-limpression-textile/